Rozpoczynając inne artykuły na naszej stronie opisujące poszczególne realizacje GRUPY WOLFF z zakresu bezpieczeństwa wybuchowego i przeciwpożarowego w przemyśle, często zaczynamy od wymienienia po krótce informacji o problemie, z którym spotkał się nasz klient na terenie swojego zakładu przemysłowego i rozwiązaniu, które dostarczyliśmy. Geneza tego artykułu jest jednak zupełnie inna…
Zapewne w jednym czy drugim miejscu na naszej stronie trafiłeś kiedyś na przynajmniej jeden z dwóch cytatów Bartosza Wolffa – prezesa GRUPY WOLFF:
Nie zawsze wszystko idzie gładko. Nigdy jednak nie zostawiliśmy naszego partnera w potrzebie. Zawsze RAZEM dążyliśmy do celu.
Nie chcemy być kolejną anonimową firmą, opartą na powierzchownych relacjach typu fast-food. W biznesie szukamy czegoś więcej – zaufania, partnerstwa i ludzkiej twarzy. To na tych fundamentach chcemy budować GRUPĘ WOLFF. Nie jest to łatwe w świecie zdominowanym przez korporacyjny, chłodny styl prowadzenia biznesu. Zapewniam jednak, że będziemy starać się podążać własną drogą. Drogą biznesu z ludzką twarzą.
Właśnie odnosząc się do słów Bartosza Wolffa, chcemy pokazać, jak może wyglądać wieloletnia współpraca z GRUPĄ WOLFF w zakresie bezpieczeństwa wybuchowego i pożarowego. Posłużymy się przykładem jednej z większych Grup Kapitałowych na polskim rynku energetycznym i ciepłowniczym.
Ochrona przeciwpożarowa kluczowych instalacji
Kiedy rozpoczęliśmy naszą współpracę z inwestorem, prawie wszystkie obiekty i budynki wymagały mniejszych lub większych modernizacji w zakresie bezpieczeństwa pożarowego i wybuchowego. Jasne było więc zarówno dla nas, jak i zarządzających w opisywanej Grupie Kapitałowej, że nie sposób jest przeprowadzić wszystkich inwestycji w jednym czasie. Nie chodziło tylko o łączny budżet wszystkich prac, które były wymagane przez rzeczoznawcę ppoż. oraz ubezpieczyciela, ale także o fakt, że zakład nie mógł pozwolić sobie na przestoje produkcyjne, gdyż dostarcza ciepłą wodę do tysięcy gospodarstw domowych w sieci ciepłowniczej jednego z największych miast w Polsce.

Fragment układu sterowania instalacją zraszaczową mostu skośnego
W związku z tym faktem inwestor podzielił konieczne do wykonania modernizacje na wiele etapów, które miały być zrealizowane w ciągu kilku lat. Przedstawione poniżej cztery z nich można zaliczyć do tych o kluczowym znaczeniu dla bezpieczeństwa przeciwpożarowego całego obiektu. Wykonaliśmy je w ciągu ostatnich 5 lat: rozpoczynając od ochrony zraszaczowej mostu skośnego wykonanej w 2018 roku, na modernizacji pompowni ppoż. i wybudowaniu zbiornika wody ppoż. oddanego w 3 kwartale 2022 roku kończąc.
W ciągu tych 5 lat zdarzało się również, że inwestor, wiedząc, że ma przestarzałą pompownię, zlecał wykonanie i dostawę awaryjnego zasilania instalacji ppoż. przez osobną pompę diesla, aby bez uszczerbku na ciągłości ochrony przeciwpożarowej mógł doczekać do momentu, w którym będą mogły się rozpocząć prace związane z kompleksową modernizacją pompowni.
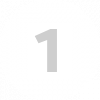
Ochrona zraszaczowa mostu skośnego
- Most skośny o długości 200 m podzieliliśmy na 12 sekcji zraszaczowych.
- Zamontowaliśmy dwie podcentrale z 12 sekcjami zraszaczowymi i doprowadziliśmy do nich zasilanie wodne
- Zabezpieczyliśmy rury mogące ulec zamarznięciu dostosowanym systemem grzania rurociągów.
- Zapewniliśmy zgodność instalacji z wytycznymi FM Global. Wszystkie komponenty posiadały dopuszczenia CNBOP.
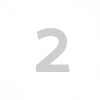
System sygnalizacji pożaru mostu skośnego
- Opracowaliśmy kompleksową koncepcję, która musiała uwzględniać wyjątkowo trudne warunki pracy powodujące ryzyko strat na skutek fałszywych alarmów.
- Zastosowaliśmy 2 niezależne linie liniowych czujek temperatury (kable sensoryczne) odpornych na zakłócenia wynikające z bardzo trudnych warunków pracy.
- Zapewniliśmy możliwość szybkiego wykrycia pożaru już na etapie tlenia się. Ograniczyliśmy tym samym potencjalne straty.
- Dostarczyliśmy różnego rodzaju sygnalizatory optyczne i akustyczne tak, aby można było natychmiastowo poinformować wszystkich pracowników o zagrożeniu, bez względu na trudne warunki pracy panujące na obiektach inwestora.
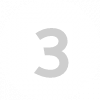
Modernizacja instalacji hydrantowej wewnętrznej
- Montaż wewnętrznej instalacji hydrantowej łączącej 11 pionów hydrantowych.
- Montaż stanowisk awaryjnego zasilania głównych pionów hydrantowych.
- Realizacja prac na czynnym obiekcie i w trudnych warunkach pracy – wysoka temperatura i duże zapylenie.
- Podnieśliśmy ciśnienie w instalacji o ponad 1 bar oraz zapewniliśmy wymaganą wydajność.
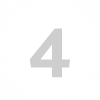
Zbiornik i pompownia wody ppoż.
- Kompleksowa modernizacja pompowni ppoż.: od zaprojektowania, przez dostawę i montaż, po prace z zakresu AKPiA oraz instalacji elektrycznych, na pracach wykończeniowych i dokumentacji kończąc.
- 2 pompy ppoż i 2 pompy typu jockey dla wody zmywnej
- Zbiornik na wodę o pojemności aż 900 m3 do celów przeciwpożarowych
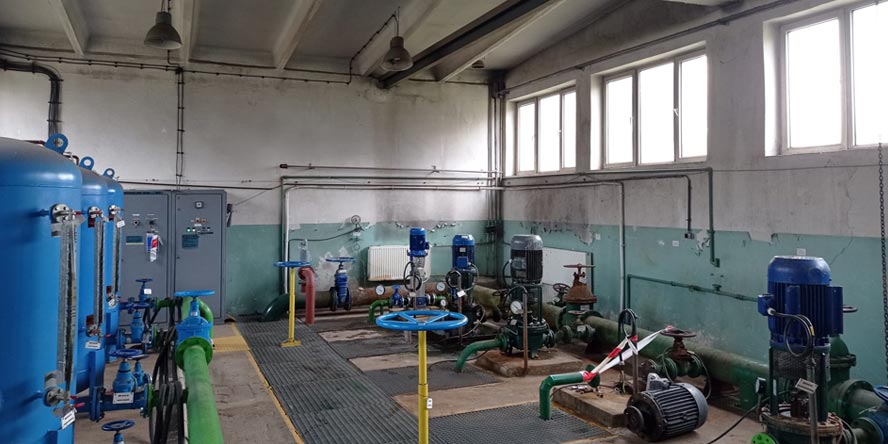
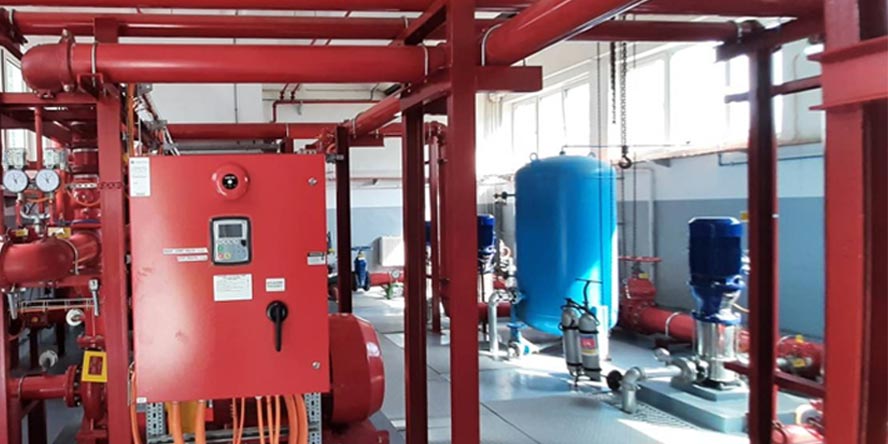
Pompownia – widok wewnątrz przed i po inwestycji (przesuń linię na zdjęciu w prawo lub lewo)
Kolejne projekty z zakresu bezpieczeństwa pożarowego
Wymienione powyżej realizacje nie były jedynymi, które w ciągu tych 5 lat współpracy wykonaliśmy na obiektach inwestora z zakresu ochrony przeciwpożarowej. Zarządzający elektrociepłownią stopniowo zwiększali bezpieczeństwo ppoż. kolejnych części swojego zakładu. Pracowaliśmy przy wielu innych zadaniach, z których warto wymienić zabezpieczenie instalacją zraszaczową zbiorników oleju, czy transformatora, oraz wykonanie instalacji oddymiania klatek schodowych i modernizację na nich oświetlenia podstawowego, awaryjnego i ewakuacyjnego.
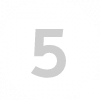
Instalacja zraszaczowa zbiorników oleju
- Cel: chłodzenie powierzchni, aby pożar był możliwy do szybkiego opanowania w chwili rozpoczęcia akcji gaśniczej.
- Pierwszy zbiornik oleju jest chroniony przez 2 poziomy zraszaczy na wysokościach 0,00m. i +5,30m.
- Drugi zbiornik chroniony jest przez zawieszone pod sufitem 3 rzędy zraszaczy po 4 dysze w każdym.
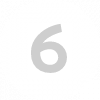
Instalacja zraszaczowa gaszenia transformatora
- Dla ochrony transformatora zaprojektowaliśmy system zraszaczy. Przepływ wody w instalacji jest uruchamiany ręcznie, po wykryciu pożaru. Wówczas zadziałają wszystkie zraszacze danej sekcji (grupy) zraszaczowej.
- Łączenie elementów rurociągów wokół transformatora zostało wykonane na połączenia szybkozłączne, aby w przypadku uzasadnionej konieczności była możliwość demontażu części pierścienia i dostęp do urządzenia.
- Istniejącą podcentralę zraszaczową rozbudowaliśmy o stację zalewową (zawór wzbudzający) wraz z zasuwą odcinającą pod stacją.
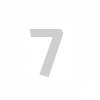
Instalacja oddymiania klatek schodowych
- W ramach projektu dostosowania budynków elektrociepłowni do wymagań przeciwpożarowych wykonaliśmy instalację oddymiania klatek schodowych.
- Dostarczyliśmy klapy dymowe z elektrycznym systemem sterowania oddymianiem, otwierane min. na kąt 140o
- Klapy podłączyliśmy do centrali sterującej gaszeniem.
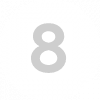
Modernizacja oświetlenia podstawowego, awaryjnego i ewakuacyjnego
- Przeprowadziliśmy modernizację oświetlenia podstawowego, awaryjnego i ewakuacyjnego klatek schodowych dwóch bloków elektrociepłowni.
- Wykonaliśmy obliczenia dotychczasowego oświetlenia wraz z wizualizacją nieprawidłowości, które należało poprawić.
- Oprócz opraw oświetleniowych zamontowaliśmy tablice oświetleniowe, łączniki oświetleniowe, puszki odgałęźne oraz instalacje ochrony od porażeń.

Zraszacz nad mostem skośnym
ATEX: Projekty z zakresu bezpieczeństwa wybuchowego
W elektrociepłowni spalany jest zarówno węgiel, jak i biomasa. Pyły tych produktów, będących źródłami energii potrzebnej do wytwarzania ciepła systemowego, są wybuchowe. W związku z tym inwestor był zobowiązany do spełnienia wymogów dyrektywy ATEX i zabezpieczenia instalacji.
Dyrektywa ATEX, wprowadzona do polskiego porządku prawnego odpowiednimi Rozporządzeniami, wymaga od pracodawcy podjęcia po kolei następujących działań:
- eliminacja powstawania atmosfer wybuchowych,
- eliminacja możliwości powstania źródła zapłonu atmosfer wybuchowych,
- zabezpieczenie instalacji przed skutkami wybuchu, czyli sprowadzenie ryzyka wybuchu i jego konsekwencji do poziomu akceptowalnego.
W przypadku zamkniętych, czy obudowanych instalacji lub ich elementów jak np. kanały, rurociągi, podnośniki kubełkowe, instalacje odpylające, można skutecznie stosować systemy minimalizujące skutki wybuchu. Tak było w przypadku instalacji spalania biomasy, kiedy to byliśmy w stanie zaproponować systemy tłumienia i izolacji wybuchu. Współpracę na tym polu rozpoczęliśmy z inwestorem już w 2012 roku, kiedy w branży energetycznej w Polsce obserwowaliśmy prawdziwy “boom” na biomasę.
Natomiast w przypadku ogromnych i otwartych przenośników węglowych na galeriach nawęglania, nie ma fizycznej możliwości, aby zastosować zaawansowane systemy przeciwwybuchowe. W takim przypadku pozostaje skupić się nad prewencją wybuchu. Polega ona na eliminacji miejsc, w których może dojść do zapłonu. Praktyka pokazuje, że zapłon może nastąpić w obrębie ogromnej ilości transportowanego materiału, jak i może być skutkiem działania wadliwych lub niedostosowanych do pracy w strefach zagrożenia wybuchem urządzeń.
Zapłon materiału transportowanego na wielkich przenośnikach może być eliminowany tylko poprzez zastosowanie systemów detekcji i gaszenia przenośników – nasze działania w tym zakresie opisaliśmy wyżej w punktach 1 i 2. Co do samych maszyn i urządzeń uczestniczących w procesie transportu materiału, należało skupić się nad poprawą ich niezawodności i dostosowaniem do wymagań ATEX – co opisaliśmy poniżej, w punkcie 9. Ostatni punkt natomiast dotyczy wspomnianego wcześniej zabezpieczenia instalacji biomasy, gdzie początek naszych prac sięga roku 2012.
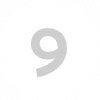
Modernizacja urządzeń i instalacji elektrycznej na obiektach nawęglania – dostosowanie do wymogów dyrektywy ATEX
- Wymieniliśmy dotychczasowe urządzenia, osprzęt i instalacje na posiadające odpowiednie certyfikaty EX i IP-5x.
- Modernizacje napędów polegały na wymianie silników napędowych wraz z reduktorami oraz bębnami napędów. Dla dwóch przenośników napędy wykonane zostały w formie motoreduktorów. Dla pozostałych napędów zaoferowaliśmy zespoły napędowe w formie zestawów: silnik indukcyjny – przekładnia stożkowo-walcowa. Zastosowane rozwiązania zagwarantowały bezawaryjną pracę przenośników w warunkach zimowych panujących na terenie naszego kraju.
- Zamontowaliśmy nowe wyłączniki linkowe wzdłuż trasy przenośników taśmowych.
- Wewnątrz przesypów zastosowaliśmy czujniki wibracyjne dla kontroli poziomu węgla. Wykorzystaliśmy dwie długości czujników w zależności od miejsca ich montażu. Zabezpieczyliśmy też czujniki odpowiednimi daszkami ochronnymi.
- Wymieniliśmy czujniki ruchu taśmy dla modernizowanych przenośników na takie, które posiadają odpowiednią cechę ATEX Ex II 1D T100°C.
- Zdemontowaliśmy stare i dostarczyliśmy nowe sygnalizatory optyczno-akustyczne.
- Wymianie podlegały także skrzynki sterowania miejscowego przenośników. Wykonaliśmy je ze skrzynek z poliwęglanu (PC) typu SOLID. Zostały wyposażone w przyciski, których układ i funkcje odwzorowaliśmy analogicznie jak w demontowanych zestawach.
- Dostarczyliśmy nowe puszki łączeniowo–rozgałęźne o odpowiednich cechach EX, które zamontowaliśmy wzdłuż linii technologicznej przenośników. Poza wyznaczonymi strefami zagrożenia wybuchem także dokonaliśmy wymiany puszek łączeniowo–rozgałęźnych, a także pomp odwodnień, łączników suwnic, skrzynek zraszaczy PV, skrzynki krosowej instalacji wodnej, oraz rozdzielnic potrzeb własnych. Do całego nowego osprzętu elektrycznego wymieniliśmy także gospodarkę kablową.
- Zmodernizowaliśmy instalację oświetlenia podstawowego i awaryjnego. W zakresie oświetlenia podstawowego wymieniliśmy istniejące oprawy oświetleniowe, które pracowały w strefie zagrożonej wybuchem, na oprawy w wykonaniu Ex (odpowiednim do strefy zagrożenia). Poza strefami Ex wymieniliśmy oprawy, aby zapewnić podwyższony stopień ochrony IP. Modernizacja oświetlenia awaryjnego także została zaprojektowana pod kątem dostosowania urządzeń do wymagań ATEX, jeżeli urządzenie pracowało w strefie zagrożenia wybuchem, lub minimalnego poziomu IP, jeżeli urządzenie pracowało poza strefą zagrożenia wybuchem.
- Wykonaliśmy próby funkcjonalne urządzeń po wymianie na obiektach nawęglania w zakresie taśm tras przenośnikowych, a także dokumentację powykonawczą, pomiarową oraz jakościową branży elektrycznej, oraz mechanicznej.
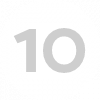
Zapewnienie bezpieczeństwa ATEX na instalacji składowania i podawania biomasy
- Historia naszej współpracy z inwestorem na instalacji składowania i podawania biomasy sięga roku 2012.
- Z początku nasze prace polegały na zamontowaniu systemów izolacji wybuchu na filtrach i tłumieniu wybuchu na podnośniku pelletu.
- W tym miejscu należy zaznaczyć, że inwestor dodatkowo zabezpieczył silos biomasy panelami dekompresyjnymi – ta część projektu przebiegała bez naszego udziału. Po pewnym czasie w bezpośrednim sąsiedztwie silosu Inwestor zbudował nowe urządzenie. Okazało się, że ewentualny wybuch w silosie sprawiłby, że rozerwane panele dekompresyjne uwolniłyby kulę ognia i fale ciśnienia wprost na to nowe urządzenie. Inwestor poprosił nas o rozwiązanie problemu. Musieliśmy dokonać zmian w taki sposób, aby wykorzystać otwory po panelach. Zdecydowaliśmy się więc na zaproponowanie systemu bezpłomieniowego odciążania wybuchu.
- Kolejnym etapem współpracy było zabezpieczenie systemem tłumienia wybuchu drugiego podnośnika kubełkowego dla zrębek.

Dostarczona sygnalizacja optyczna jako jeden z elementów modernizacji 12 przenośników do pracy w strefach Ex
Zaufanie, partnerstwo, ludzka twarz
W kontekście współpracy z opisywaną Grupą Kapitałową zapytaliśmy Bartosza Wolffa – prezesa GRUPY WOLFF o kwestie związane z jego wcześniejszymi wypowiedziami dotyczącymi fundamentów prowadzenia firmy i współpracy z klientami. Oto co od niego usłyszeliśmy:
“Jeśli mamy mówić o wartościach i fundamentach naszej współpracy z klientami, czy też tym konkretnym klientem, to konieczne jest przywołanie jeszcze jednej mojej wypowiedzi, którą można znaleźć na naszej stronie, a dokładnie w zakładce “kariera”. Otóż chodzi o to, że nie ma firm idealnych – i my też nie jesteśmy takim utopijnym przedsiębiorstwem. Przepracowanie w sobie tego banalnego wręcz faktu potrafi zmienić perspektywę relacji pomiędzy partnerami w biznesie. Otwiera oczy i uszy na potrzeby innych, pozwala wsłuchać się w drugą stronę, czyli jest fundamentem, na którym można budować takie ludzkie, partnerskie relacje, a nie jak to kiedyś określiłem fast-foodowy biznes.
Przechodząc do konkretów, chyba najlepszym przykładem, którym mogę się posłużyć, jest historia zabezpieczenia silosu biomasy. Pierwotnie inwestor nie montował paneli dekompresyjnych przy naszym udziale, a także nie konsultował z nami wpływu zastosowanego systemu odciążającego na nowo budowane urządzenie. Kiedy je postawił, było, kolokwialnie mówiąc, już “po ptakach”.
Czy do tego momentu mogliśmy zrobić coś lepiej jako GRUPA WOLFF? Z perspektywy czasu mogę powiedzieć, że oczywiście, że tak. Widząc istniejące już zabezpieczenia w postaci paneli, mogliśmy się upewnić, że nasz partner zna wszystkie zalety i wady rozwiązania, które zastosował. Przede wszystkim, że jest świadomy, że w pobliżu paneli nie wolno mu budować nowych instalacji, które byłyby wówczas zagrożone w momencie wybuchu i rozerwania paneli. Od tej pory podczas różnych spotkań zawsze staramy się wychodzić z dodatkową inicjatywą i poszerzać wiedzę naszego klienta z zakresu ppoż. i ATEX.
Wracając jednak do omawianego projektu… oczywiste było, że nie zostawiliśmy naszego partnera w potrzebie. Musieliśmy zaproponować inny układ z zakresu bezpieczeństwa wybuchowego, który z jednej strony będzie niwelował skutki wybuchu do wnętrza chronionego silosu, a z drugiej wykorzysta istniejące w silosie otwory po panelach dekompresyjnych. Zaproponowaliśmy zastosowanie układów bezpłomieniowego odciążania wybuchu. Montaż realizowaliśmy na wysokości 35 metrów, przez co prace wymagały od nas użycia specjalistycznego sprzętu oraz dostępu linowego. I choć gabaryty nowych elementów były dobrane precyzyjnie – dosłownie na „milimetry” – to odpowiednie przygotowanie do montażu pozwoliło nam go zrealizować w ciągu jednego dnia.”