Unikalna instalacja przeciwwybuchowa, którą zaprojektowaliśmy dla międzynarodowego producenta dodatków spożywczych łączy prewencję i izolację wybuchu zgodnie z ATEX. W ten sposób skutecznie zabezpieczyliśmy przed wybuchem nie tylko mielenie celulozy, ale ciągłość pracy całego zakładu. A do tego ograniczyliśmy koszt całkowity inwestycji!
Wyzwanie
- Przetwarzanie (w tym mielenie) celulozy powoduje wysokie ryzyko wybuchowe i pożarowe.
- Częste aktywacje instalacji tłumienia i odprzęgania wybuchu generowały koszty.
- Klient chciał zmodyfikować istniejący system ochrony przeciwwybuchowej tak, aby zredukować koszty, a jednocześnie zachować najwyższy poziom bezpieczeństwa w zakładzie.
- Montaż był możliwy jedynie w trakcie zaplanowanego, jednodniowego przestoju produkcyjnego.
Rozwiązanie
- Zaprojektowaliśmy spójny system ochrony przeciwwybuchowej, który pozwolił zredukować ryzyko do poziomu akceptowanego przez klienta
- Nasza koncepcja uwzględniała rozwiązania niedostępne u konkurencji
- Zaproponowane rozwiązanie pozwoliło ograniczyć całkowity koszt utrzymania rozwiązania (TCO) o 35%
- Klient zadecydował o wdrożeniu bliźniaczego systemu zabezpieczenia młyna (nazwanego żartobliwie „Shrekiem”) również w innych zakładach w Europie.
Nasz klient to międzynarodowa grupa firm specjalizująca się w produkcji dodatków spożywczych, przede wszystkim włókien celulozy. Ich produkty są kluczowym składnikiem m.in. jogurtów, a ich zakłady działają na kilku europejskich rynkach. Przy tej skali produkcji ciągłość procesów jest kluczowa – jednak produkt, który powstaje w zakładzie nie ułatwia zadania.
Celuloza: niepozorne źródło zagrożenia wybuchem
Celuloza – bo o niej mowa – jest substancją, która stwarza bardzo wysokie ryzyko pożarowe i wybuchowe. W sześciostopniowej skali palności (BZ1-BZ6), celuloza ma palność na poziomie BZ5, a zapala się już w 340°C. Do zapłonu cząstek celulozy wystarczy 30–100 mJ – tyle wynosi minimalna energia zapłonu (MEZ) tej substancji.
Gdy pył celulozy wybuchnie, eksplozja jest na tyle poważna, że może powodować zniszczenia budynków, uszkodzenia ciała (np. płuc), a nawet śmierć ludzi przebywających w pobliżu (współczynnik wybuchowości celulozy (Kst) wynosi 50-150 [bar*m*s-1], a maksymalne ciśnienie wybuchu sięga 11,5 bar). Nic więc dziwnego, że podczas przetwarzania takiego surowca, jak celuloza bezpieczeństwo procesowe jest szczególnie ważne.
Mielenie celulozy: na czym polega zagrożenie?
Celuloza przyjeżdża do zakładu klienta w formie brykietów, które trafiają do młyna. Tam jest rozdrabniana do postaci drobnego pyłu, który można transportować pneumatycznie. Za pomocą pneumatycznego sytemu transportowego rozdrobiona celuloza trafia separatora mechanicznego tzw. cyklonu, skąd jest odbierana i pakowana do dalszego transportu. Najdrobniejsza frakcja pyłu, która wydostanie się z cyklonu, przechodzi poprzez kanały odpylające do filtra workowego.
Na każdym etapie procesu przetwarzania celulozy klient ma więc do czynienia z pyłem, który przy niesprzyjających warunkach może zapalić się i wybuchnąć. Przy odpowiednich warunkach zapłon pyłu celulozy może wywołać nawet iskra elektrostatyczna z ludzkiego ciała (która ma energię ok. 10–30 mJ).
Optymalizacja systemu HRD potrzebna od zaraz
Dotychczas instalację mielenia i odpylania chronił niezwykle skuteczny system tłumienia i odprzęgania wybuchów typu HRD (High Discharge Rate). Wczesne oznaki wybuchu – ciśnienie lub płomień – wykrywają czujniki umieszczone w środku chronionych urządzeń. W ułamku sekundy sygnał trafia do centrali sterującej, która natychmiast aktywuje butle z czynnikiem gaśniczym. Gaśnica HRD wyrzuca środek tłumiący pod wysokim ciśnieniem bezpośrednio do wnętrza instalacji i w ten sposób zatrzymuje rozwój wybuchu jeszcze w jego zarodku. Jednocześnie centrala aktywuje zawory odprzęgające, które zabezpieczają sąsiadujące elementy linii technologicznej przed przeniesieniem fali ciśnienia i płomienia.
Ze względu na wybuchowość celulozy system HRD generował jednak znaczące koszty. Wynikały one z częstych aktywacji, które powodowały przestoje produkcyjne urządzeń. Zwłaszcza te ostatnie skutki były dla klienta wyjątkowo uciążliwe, ponieważ każdy dzień opóźnienia w produkcji groził utratą kluczowych kontraktów.
Klient chciał zmodyfikować więc istniejący system zabezpieczeń przeciwwybuchowych tak, aby móc zredukować koszty jego obsługi, a jednocześnie zachować najwyższy poziom bezpieczeństwa w zakładzie.
Jak przekonaliśmy klienta do inwestycji w bezpieczeństwo Ex
Eksperci ds. bezpieczeństwa naszej firmy przeprowadzili szczegółowe analizy oraz bezpośrednie konsultacje z zarządem klienta, by uzyskać pełny obraz sytuacji. Na tej podstawie opracowali innowacyjną koncepcję, która – choć wcale nie była najtańsza (!) – przekonała inwestora.
Zastosowaliśmy w niej rozwiązanie niedostępne u konkurencji, które w znaczący sposób obniżało koszty projektu oraz późniejsze koszty utrzymania rozwiązania. Oprócz tego nasze rozwiązanie pozwoliło zmodyfikować system zabezpieczeń przed propagacją wybuchów wtórnych w zakładzie tak, by zapewniało ono ochronę życia pracowników i urządzeń, a także zgodność z Dyrektywą ATEX.
Zobacz, jak zredukowaliśmy koszty i ryzyko biznesowe związane z częstymi aktywacjami systemu HRD!
Nowe podejście do zabezpieczenia urządzeń do mielenia celulozy
Mielenie to proces, który generuje niezwykle wysokie ryzyko wybuchowe i pożarowe, ponieważ drobne cząstki pyłu mogą łatwo tworzyć chmury wybuchowe. Najczęstszą przyczyną eksplozji w młynach jest zaciągnięcie obcego elementu wraz z produktem lub poprzez czerpnie powietrza, który w trakcie burzliwego ruchu surowca w młynie powoduje iskrzenie.
Młyn klienta był już zabezpieczony butlami HRD, jednak słabym punktem urządzenia były dwie niezabezpieczone czerpnie powietrza do młyna oraz jedna czerpnia powietrza do systemu transportu pneumatycznego. W przypadku wybuchu, przez te pozornie niewielkie kanały, kula ognia i ciśnienia mogła wydostać się z młyna na halę produkcyjną i spowodować serię wybuchów wtórnych, które mogły wyrządzić poważne straty. Aby temu zapobiec, zaproponowaliśmy, że na każdej z czerpni zamontujemy zawór izolujący IsoDisc.
Zawór mechaniczny IsoDisc to pasywne urządzenie izolacyjne. W normalnych warunkach pracy przepływ powietrza procesowego utrzymuje płytę zaworu IsoDisc w pozycji otwartej. W przypadku wybuchu w urządzeniu nagły wzrost ciśnienia automatycznie zamyka IsoDisc, a co za tym idzie – izoluje stronę procesu i ogranicza rozprzestrzenianie się płomienia oraz ciśnienia do połączonych urządzeń lub otoczenia. Rozwiązanie jest zgodne z normą EN15089.
Nasze rozwiązanie zostało ochrzczone mianem „Shrek”, ponieważ zawory IsoDisc zainstalowane na czerpniach młyna przypominają postać bajkowego ogra!
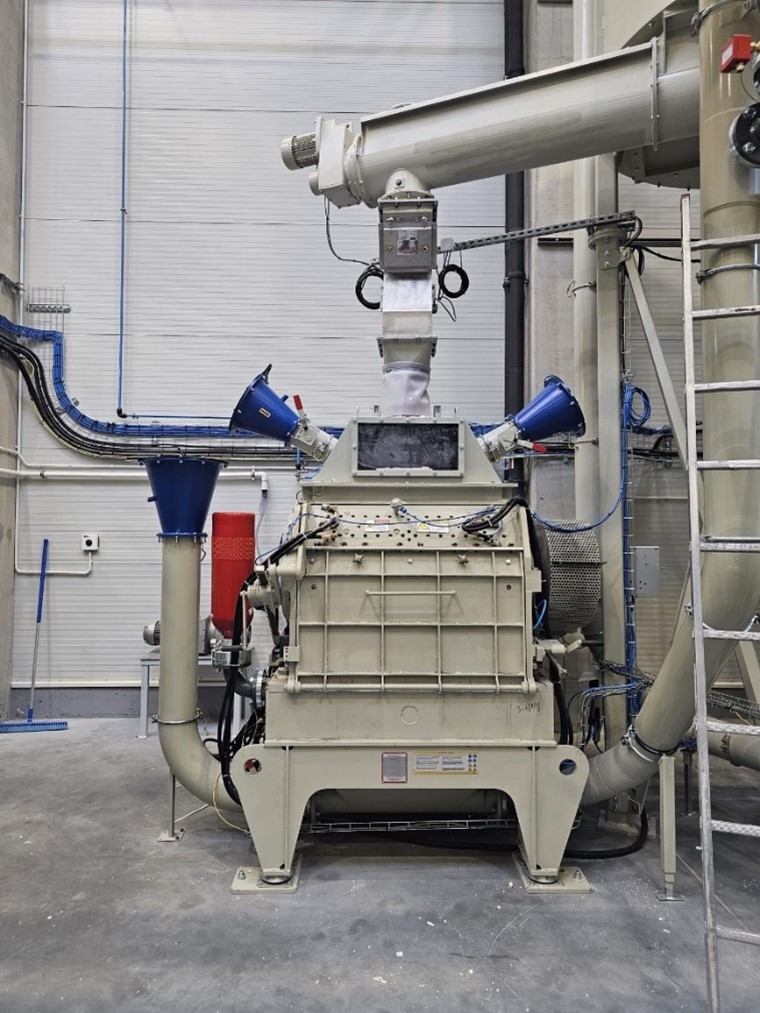
Zabezpieczenie instalacji transportu pneumatycznego pyłu celulozy
Jako eksperci od bezpieczeństwa procesowego skupiamy się nie tylko na ograniczaniu możliwości pojawienia się atmosfery wybuchowej, ale także na eliminowaniu potencjalnych źródeł zapłonu.
W przypadku naszego klienta tym źródłem zapłonu są zwłaszcza żarzące się cząstki celulozy, które powstają w procesie mielenia surowca. Wydostają się one z młyna do dalszej części instalacji i powodują aktywacje systemu HRD. Aby temu zapobiec, zaproponowaliśmy system detekcji i gaszenia iskier Atexon na rurze transportowej.
System Atexon ma detektor promieniowania podczerwonego, który wykrywa iskry czy gorące cząstki i natychmiast uruchamia gaszenie. Proces ten jest dostosowywany do ilości i rodzaju źródeł zapłonu (w tym przypadku cząstek celulozy), a jednocześnie nie zakłóca procesu produkcji. Zobacz, jak rozwiązaliśmy bardzo podobny problem u innego producenta spożywczego, montując system gaszenia iskier dla instalacji odpylania herbaty.
Dodatkowo na systemie rur odprowadzających powietrze z cyklonu do filtra zaprojektowaliśmy klapy zwrotne. Ich rolą jest zabezpieczyć układ pneumatyczny przed ewentualnym cofnięciem się wybuchu. Zjawisko to prowadzi do powstania dużo groźniejszych w skutkach wybuchów wtórnych – eksplozje te mogą spowodować całkowite zniszczenie instalacji.
Katastrofa w Imperial Sugar: winowajcą wybuchy wtórne
Wybuch w cukrowni Imperial Sugar w Port Wentworth (Georgia, USA) z 2008 roku do dziś stanowi tragiczne przypomnienie o konieczności stosowania skutecznej ochrony przeciwwybuchowej w zakładach przemysłowych. W wyniku eksplozji pyłu cukrowego zginęło 14 osób, a dziesiątki zostało rannych – wszystko to wydarzyło się w przestrzeniach zagrożonych wybuchem, gdzie zabrakło odpowiednich zabezpieczeń i nadzoru nad warunkami pracy.
Zobacz skalę zniszczeń, jaką spowodowały wybuchy wtórne w cukrowni:
Jak pokazuje przykład Imperial Sugar, w strefach Ex każda iskra może stanowić realne zagrożenie. Pracownicy cukrowni działali w przestrzeniach zagrożonych wybuchem, jednak ani infrastruktura ani procesy w zakładzie nie były nastawione na minimalizowanie ryzyka. To tragiczne zdarzenie dobitnie pokazuje, jak kluczowa jest precyzyjna ocena ryzyka oraz wdrożenie kompleksowych systemów ochrony przeciwwybuchowej wszędzie tam, gdzie występuje pył organiczny.
Jak zoptymalizować koszt rozwiązań przeciwwybuchowych?
Aby zaproponować najkorzystniejsze dla klienta rozwiązanie przeciwwybuchowe, bierzemy pod uwagę nie tylko czynniki procesowe i techniczne, które pozwalają spełnić wymagania Dyrektywy ATEX.
Zwracamy także uwagę na koszty, i to w pełnym ujęciu – nie tylko przy zakupie i instalacji, ale także w ciągu całego „cyklu życia” rozwiązania (tzw. Total Cost of Ownership (TCO)). Takie podejście pozwala klientowi rzetelnie porównać naszą propozycję z rozwiązaniami konkurencji.
Aby obliczyć Total Cost of Ownership zabezpieczenia przeciwwybuchowego trzeba wziąć pod uwagę:
- koszty zakupu poszczególnych komponentów i ich instalację oraz uruchomienia całego systemu
- koszty dorocznego przeglądu
- koszty związane z przywróceniem instalacji po aktywacji
Zobacz, jak możesz oszacować, ile naprawdę kosztuje instalacja przeciwwybuchowa:
Właśnie z myślą o optymalizacji wydatków zaproponowaliśmy naszemu klientowi zabezpieczenie, które pozwala zachować pełną zgodność z przepisami i normami, a jednocześnie tańsze w utrzymaniu. Zgodnie z Dyrektywą ATEX nasz klient miał dwie opcje ochrony przeciwwybuchowej młyna:
- Instalacja przeciwwybuchowa 1: IsoDisc x 3 + 2 butle HRD (istniejące)
- Instalacja przeciwwybuchowa 2: 5 butli HRD (2 istniejące + 3 nowe)
Zabezpieczenie czerpni powietrza w młynie celulozy za pomocą systemu HRD zamiast IsoDisków wymagałoby zainstalowania trzech dodatkowych butli HRD. Dopiero taka ilość środka gaśniczego byłaby wystarczająca do stłumienia wybuchu. Jeżeli czerpnie pozostałyby niezabezpieczone – część proszku wydostawałby się wtedy na zewnątrz pod wpływem ciśnienia z aktywowanych butli.
Aby pokazać skalę oszczędności pomiędzy tymi dwoma propozycjami przyjęliśmy, że:
- Koszt zakupu i instalacji komponentów do obu systemów jest porównywalny.
- Koszt dorocznego przeglądu będzie w obu wariantach porównywalny.
Zmienną, która decyduje o różnicy w TCO między sposobem 1 i 2 to koszt przywrócenia systemu do pracy po ewentualnej aktywacji. W przypadku sposobu 1 (IsoDisc + HRD) regeneracji wymaga 2 z 5 elementów systemu. Z kolei sposób 2 (5 x HRD) wymaga regeneracji wszystkich elementów.

Przy założeniu, że koszt przywrócenia 1 elementu = X, można obliczyć, że zastosowanie IsoDisków przyniosło oszczędności o ok. 35%:
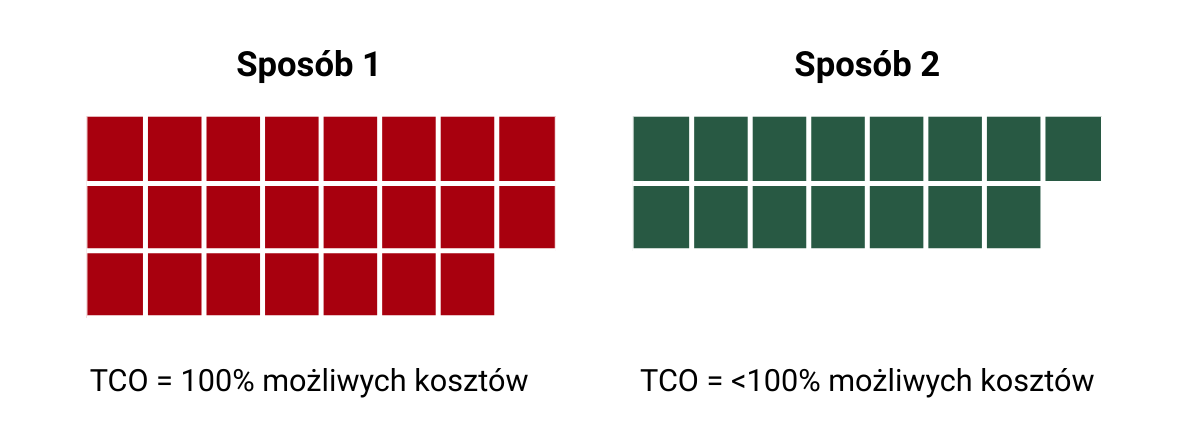
W jaki sposób IsoDisk pozwolił ograniczyć koszt całkowity rozwiązania Ex?
- Po pierwsze, jest to rozwiązanie mechaniczne, wielokrotnego użytku, które nie wymaga ingerencji serwisowej po zadziałaniu.
- Po drugie, IsoDisk wzmacnia działanie już zainstalowanego na młynie systemu HRD. Zamykając się pod wpływem ciśnienia wybuchu, zawór zatrzymuje w środku młyna środek gaśniczy z butli HRD, dzięki czemu może on zadziałać z pełną skutecznością w mniejszej ilości.
Montaż zabezpieczeń przeciwwybuchowych: precyzyjne planowanie to błyskawiczne wykonanie
Wdrożenie rozwiązań wymagało modyfikacji instalacji odpylania. Prace te zrealizowaliśmy w zaledwie jeden dzień, podczas zaplanowanego przestoju. Dzięki ścisłej współpracy z działem utrzymania ruchu i produkcją, precyzyjnie zaplanowaliśmy zakres działań w taki sposób, aby maksymalnie ograniczyć wpływ montażu systemów ochrony przeciwwybuchowej na bieżącą działalność zakładu.
Nasz zespół działał w ściśle wydzielonych strefach, poruszając się wyłącznie w miejscach udostępnionych przez klienta. Zabezpieczyliśmy wszystkie urządzenia i elementy instalacji, które mogłyby ulec zanieczyszczeniu lub uszkodzeniu podczas prac. Przestrzegaliśmy rygorystycznych standardów ochrony zarówno ludzi, jak i infrastruktury, mając świadomość, że każda godzina przestoju w zagrożonej wybuchem instalacji to realne zagrożenie dla ciągłości produkcji. Po zakończeniu montażu teren został posprzątany i przywrócony do pełnej pracy, co pozwoliło klientowi błyskawicznie uruchomić linię bez zakłóceń.
Shrek sprawdził się i w Polsce, i w Belgii
Mielenie celulozy to jak oswajanie smoka: ryzyko jest potężne, a żeby się zabezpieczyć, trzeba ponieść spore koszty. Ale jak pokazuje przykład naszego klienta, nie zawsze tak musi być. Dzięki całościowemu spojrzeniu na bezpieczeństwo procesowe udało nam się osiągnąć najważniejsze dla klienta cele: znacząco ograniczyć ryzyko wybuchowe, a co za tym idzie ochronę życia ludzkiego oraz majątku firmy. Zrealizowaliśmy także drugi ważny dla klienta cel: pomogliśmy ograniczyć koszty wynikające z nieuzasadnionych aktywacji systemu zabezpieczeń.
Korzyści z wdrożenia w polskim zakładzie zachęciły klienta do zainstalowania bliźniaczego „Shreka” również w zakładzie w Belgii. Mamy nadzieję, że uda nam się wspierać w zakresie bezpieczeństwa wybuchowego kolejne inwestycje klienta – nie tylko w Polsce, ale i w Europie, USA, Kanadzie czy Australii.
Bezpieczeństwo ATEX produkcji spożywczej: znamy się na tym
Jako GRUPA WOLFF dobrze znamy problemy, z jakimi zmagają się firmy działające w branży spożywczej. Jako GRUPA WOLFF dobrze znamy problemy, z jakimi zmagają się firmy działające w branży spożywczej. Dla jednego z dużych producentów cukru opracowaliśmy spójny system bezpieczeństwa przeciwwybuchowego, który spełniał aż 22 zalecenia wskazane w Dokumencie Zabezpieczenia przed Wybuchem (DZPW).
Mamy wieloletnie doświadczenie w projektowaniu i wdrażaniu instalacji w przestrzeniach zagrożonych wybuchem – zarówno w nowych zakładach, jak i podczas modernizacji istniejących urządzeń. Zdajemy sobie sprawę, jak istotne jest utrzymanie ciągłości pracy w strefach Ex oraz skuteczna eliminacja zagrożenia w miejscach, gdzie przetwarza się łatwopalne pyły i substancje organiczne, takie jak celuloza. Dlatego nasze rozwiązania w zakresie ochrony przeciwwybuchowej są nie tylko zgodne z Dyrektywą ATEX, ale również zoptymalizowane pod kątem całkowitego kosztu eksploatacji i łatwości serwisowania.
Nasi inżynierowie regularnie przeprowadzają audyty bezpieczeństwa wybuchowego, identyfikując potencjalne źródła zagrożenia w przestrzeni zagrożonej wybuchem oraz rekomendując optymalne środki ochrony dla pracowników.
Potrzebujesz sprawdzonego partnera, który pomoże Ci zabezpieczyć linię produkcji spożywczej w założonym czasie i ramach budżetowych? Zapraszamy do kontaktu – nasi eksperci doradzą, jak najszybciej możesz poprawić bezpieczeństwo wybuchowe w swoim zakładzie, a w dodatku mogą pomóc Ci zdobyć finansowanie zabezpieczeń ATEX!