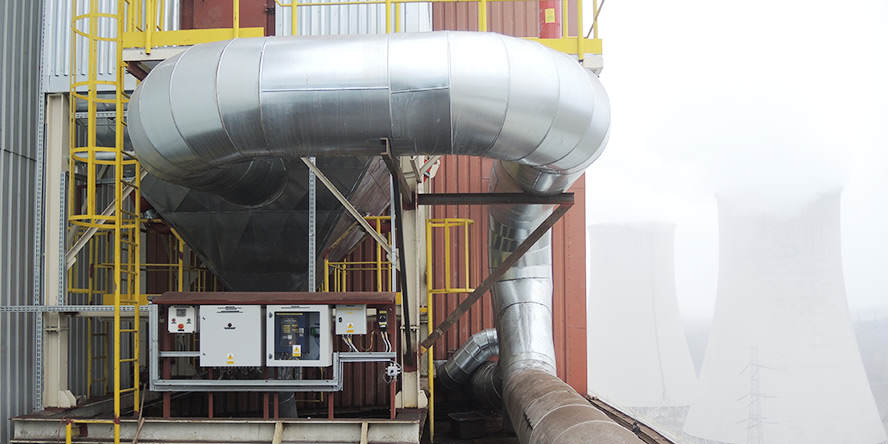
Wprowadzenie
Większości procesom technologicznym w zakładach przemysłowych zajmujących się produkcją towarzyszy zjawisko wytwarzania oraz emisji pyłów, które mają niekorzystny wpływ na otoczenie, a w przypadku pyłów tworzących z powietrzem mieszaniny wybuchowe mogą stwarzać potencjalne zagrożenie wybuchowe.
Do najbardziej pyłotwórczych procesów należą procesy: kruszenia, mielenia, przesiewania, mieszania materiałów, transportowe a także wydobywania surowców. Do znacznej ilości wydzielających się gazów i pyłów dochodzi także w trakcie produkcji np. stali w elektrycznych piecach łukowych czy trochę mniej w piecach indukcyjnych. Z kolei najbardziej szkodliwe pyły wysokodyspersyjne w dużych stężeniach powstają w trakcie procesów ostrzenia, szlifowania czy polerowania.
Zagrożenie zdrowia i bezpieczeństwa osób pracujących w zapylonym środowisku zależy od rodzaju substancji tworzących pył, jego stężenia w powietrzu, wielkości i kształtu cząstek, rozpuszczalności w cieczach organicznych oraz struktury krystalicznej pyłu. Szkodliwe działanie pyłu na człowieka może mieć charakter:
- drażniący (cząstki węgla, żelaza, szkła, aluminium, związku baru, itp.)
- zwłókniający (cząstki kwarcu, azbestu, talku, kaolinu, pyły rud żelaznych i węgla),
- kancerogenny (azbest, ogniotrwałe włókna ceramiczne, pyły drewna twardego buku i dębu),
- alergizujący (pyły pochodzenia roślinnego, zwierzęcego, leki, pyły arsenu, miedzi, cynku, chromu).
Tak szerokie spektrum szkodliwego działania pyłu na człowieka wymusza działania zmierzające do skutecznego ich ograniczania lub eliminowania na stanowiskach pracy.
Problematyka zwalczania zapylenia w dużym uproszczeniu sprowadza się w zasadzie do rozwiązania kilka podstawowych zagadnień:
- ograniczenia ilości powstających pyłów
- maksymalnego ujęcia emitowanych zanieczyszczeń pyłowych,
- dokładnego ich oczyszczenia w urządzeniach odpylających w stopniu pozwalającym na emisję odpylanych gazów do atmosfery
O ile oczyszczenie odciąganych gazów na obecnym etapie rozwoju techniki odpylania można uznać w dużym stopniu za rozwiązane, o tyle zagadnienie ograniczenia ilości powstających pyłów a przede wszystkim ich ujęcia stanowi nadal problem otwarty w skali ogólnoświatowej, przy czym posiada ono istotną rolę w zakresie uzyskania ogólnej skuteczności instalacji odpylającej.
Konieczność ograniczania zapylenia w miejscach jego powstawania inspiruje technologów do ciągłego doskonalenia procesów technologicznych zmierzających do ograniczenia ilości powstających w ich trakcie pyłów. Przykładem może być ograniczanie zapylenia w kopalniach przez stosowanie układów zraszających na kombajnach ścianowych czy chodnikowych, stosowanie dysz zraszających na przesypach przenośników z urobkiem czy stosowanie tzw. kurtyn wodnych. Należy zwrócić uwagę, że zraszanie przesypów przenośników zapoczątkowane w kopalniach jest coraz częściej wykorzystywane w innych gałęziach przemysłu. Z kolei w przemyśle drzewnym zmniejszenie ilości emitowanych pyłów odbywa się przez dobór odpowiednich parametrów obróbki drewna, właściwe przygotowanie narzędzi pracy, czy zastępowanie szlifowania innymi rodzajami obróbki wygładzającej.
Zasadnicze znaczenie ma jednak zwalczanie zapylenia przez stosowanie sprawnie działających instalacji: mechanicznej wentylacji wywiewnej oraz instalacji i urządzeń odciągów miejscowych wyposażonych w odpylacze.
Zarówno w systemach wentylacji ogólnej jak i w urządzeniach wentylacji miejscowej elementami odpowiedzialnymi za jakość powietrza wywiewanego są systemy oczyszczające wyposażone w odpowiednie odpylacze.
Początki rozwoju techniki odpylania możemy prześledzić wg poniższego kalendarium na poniższych przykładach.
POCZĄTKI PRODUKCJI URZĄDZEŃ ODPYLAJĄCYCH – KALENDARIUM
1821
Nauczyciel matematyki M. Hohlfeld z Lipska po raz pierwszy opisał wytrącanie się cząsteczek dymu w metalowej rurze z powodu elektrostatyczności.
1884
Oliver Lodge, brytyjski fizyk i wynalazca, odkrył możliwości zastosowania pola elektrostatycznego do oczyszczania powietrza z pyłów i dymów. Ideę filtrów elektrostatycznych zaprezentował na wykładzie w Montrealu w 1884 roku.
1906
Fryderyk Gardner Cottrell, amerykański chemik fizyczny, opracował zasady działania elektrofiltru i przedstawił je na Uniwersytecie Kalifornijskim w Berkeley.
1908
Gardner Cottrell buduje w fabryce kwasu siarkowego elektrofiltr rurowy wykorzystujący transformator z prostownikiem mechanicznym.
1912
Budowa elektrofiltru płaskiego z wyraźnym ulotem (E. Moeller).
1923
W Detroit w Michigan wybudowano elektrofiltr do oczyszczania spalin pochodzących z kotła energetycznego (4 lata po wprowadzeniu techniki spalania pyłu węglowego w kotłach energetycznych). 1940 w Hucie Łaziska zainstalowano 2-stopniowy układ odpylania składający się osadczej komory rozprężnej i elektrofiltru. Skuteczność odpylania sięgała około 95-97% – była to bardzo nowoczesna konstrukcja. 1952 ELWO Pszczyna wykonuje pierwsze elektrofiltry na potrzeby krajowe.
W MIĘDZYCZASIE ROZWIJA SIĘ PRODUKCJA SUCHYCH ODPYLACZY TKANINOWYCH I TAK PRZYKŁADOWO:
1919
W Niemczech powstaje firma Neotechnik produkująca (do dzisiaj) filtry kieszeniowe czyszczone sprężonym powietrzem lub powietrzem z wentylatora.
1954
Firma Kowent jako pierwsza w Polsce zaczyna produkcję filtrów i innych elementów instalacji odpylających.
Z KOLEI POCZĄTKI ODKURZACZA TO ROK 1901, KIEDY TO:
1901
Brytyjczyk Hubert Booth wymyślił i opatentował odkurzacz elektryczny. Udoskonalając swój wynalazek stworzył odkurzacz przewoźny (ciągnięty przez konie), który wynajmował klientom.
1908
Amerykanin Murray Spangler stworzył i opatentował małe elektryczne odkurzacze domowe. Do II wojny światowej było to urządzenie cenne i luksusowe. Do powszechnego użytku weszło dopiero w latach 40 i 50 XX wieku.
Aspekty prawne
Początki przepisów prawnych dotyczących zapylenia i zadymienia powietrza atmosferycznego istniały już w czasach średniowiecznych. W roku 1273 król angielski Edward I zakazał stosowania węgla jako paliwa ze względu na szkodliwy dym, który się przy tym wydzielał, i wyznaczył wysokie kary dla tych, którzy uchylali się od wykonania zarządzenia. Kolejne akty prawne w Anglii i na świecie dotyczyły przede wszystkim ochrony powietrza atmosferycznego przed nadmierną emisją gazów i pyłów. W Anglii w 1863 uchwalono tzw. Alkali Akt, który nakazywał wyłapywanie co najmniej 95% chlorowodoru (HCL) wytwarzanego w trakcie rozkładu soli alkalicznych preparowanych za pomocą kwasu siarkowego. W 1882 roku w Chicago wydano pierwszy akt prawny ograniczający emisję pyłów. Obecne akty prawne szczegółowo regulują wielkości dopuszczalnych wielkości zanieczyszczeń wprowadzanych do atmosfery – Rozporządzenie Ministra środowiska z dnia 22 kwietnia 2011r. w sprawie standardów emisyjnych z instalacji. Dz. U nr 95 poz. 558.
W kręgu naszego zainteresowania znajduje się jednak zapylenie wewnątrz zakładów przemysłowych i możliwości jego ograniczania.
Zagadnienie dopuszczalnego zapylenia wewnątrz hal produkcyjnych (na stanowiskach pracy) regulują ustalone normy dopuszczalnych koncentracji. W Polsce pierwszym aktem prawnym regulującym te zagadnienia było wydane w 1959 roku Rozporządzenie Prezesa Rady Ministrów z dnia 21 sierpnia (Dz. U. Nr 53, poz. 316) w którym podano obowiązujące u nas dopuszczalne koncentracje w zakładach przemysłowych.
Obecnie obowiązujące wymagania zapewniające bezpieczne i higieniczne warunki pracy zawarto w kodeksie pracy, rozporządzeniach ministrów infrastruktury, pracy i polityki socjalnej, Polskich Normach, dyrektywach Wspólnoty Europejskiej i innych dokumentach:
- Kodeks Pracy znowelizowany ustawa z dnia 14listopada 2004 r. o zmianie ustawy (Dz. U. nr 213, poz. 208). Zmiany te dostosowują polskie prawo pracy do dyrektyw socjalnych Unii Europejskiej, a zwłaszcza do kluczowej Dyrektywy Ramowej 89/391/EWG, która ustanawia serię ogólnych zasad postępowania w dziedzinie ochrony zdrowia i bezpieczeństwa pracy. Przepisy kodeksu pracy oraz aktów wykonawczych do tej ustawy charakteryzują się tym, że mają one charakter prawa bezwzględnie obowiązującego.
- Rozporządzenie Ministra Infrastruktury z dnia 12 kwietnia 2002r. w sprawie warunków technicznych jakim powinny odpowiadać budynki i ich usytuowanie. Dz. U. nr 75, poz. 690
- Rozporządzenie Ministra Pracy i Polityki Socjalnej z dnia 26 września 1997 r. w sprawie ogólnych przepisów bezpieczeństwa i higieny pracy Dz. U. nr 129, poz.844 ze zmianami
- Rozporządzenie Ministra Pracy i Polityki Socjalnej z dnia 29 listopada 2002r.r. w sprawie najwyższych dopuszczalnych stężeń i natężeń czynników szkodliwych dla zdrowia w środowisku pracy. Dz. U. nr 217, poz. 1833.Wykazano tu wartości prawnie obowiązujące dla wszystkich gałęzi przemysłu w Polsce. Stanowią one podstawowe kryterium oceny narażenia i ryzyka zawodowego związanego z obecnością szkodliwych czynników w środowisku pracy.
- Rozporządzenie Ministra Gospodarki z dnia 8 lipca 2010 r. w sprawie minimalnych wymagań dotyczących bezpieczeństwa i higieny pracowników zatrudnionych na stanowiskach pracy, na których może wystąpić atmosfera wybuchowa. Dz. U. 2010 nr 138 poz. 931
Porównując wymagania prawne z 1959 roku z obecnymi możemy stwierdzić drastyczne zaostrzenie wymagań – nawet kilkukrotne obniżenie NDS ( Najwyższe Dopuszczalne Stężenie) na stanowiskach pracy, oraz uszczegółowiony wykaz pyłów szkodliwych. Przepisy wymuszają zatem szereg działań mających na celu eliminowanie zanieczyszczeń powietrza w pomieszczeniach i na stanowiskach pracy. Ze względu na wysoką szkodliwość zanieczyszczeń powietrza w tym zapylenia powinno być ono eliminowane – jeżeli jest to możliwe, lub zmniejszane w pozostałych przypadkach przez stosowanie różnych rozwiązań technicznych ( zmiany w technologii,maszyn czy materiałów), organizacyjnych czy w końcu stosowanie wentylacji miejscowej wywiewnej.
Zakłady, które prowadzą instalacje mogące powodować znaczne zanieczyszczenie środowiska muszą uzyskać Pozwolenie zintegrowane. Ponadto instalacje te powinny spełniać wymagania ochrony środowiska wynikające z najlepszych dostępnych technik (BAT) oraz nie mogą powodować przekroczeń granicznych wielkości emisji, dotyczy to zarówno środowiska pracy jak i atmosfery.
Obowiązek uzyskania pozwolenia zintegrowanego mają instalacje z różnych gałęzi gospodarki np:
- przemysłu energetycznego: instalacje do spalania paliw o mocy nominalnej ponad 50MWt,
- hutnictwa i przemysłu metalurgicznego m.in.:
- instalacje do odlewania metali żelaznych, o zdolności produkcyjnej ponad 20ton wytopu na dobę,
- instalacje do produkcji masy włóknistej z drewna lub innych materiałów włóknistych,
Pozwolenie zintegrowane jest to jedna decyzja administracyjna, będąca szczegółową licencją na prowadzenie całej instalacji. Brak pozwolenia zintegrowanego jest równoznaczny z zamknięciem obiektu i zaprzestaniem działalności gospodarczej.
Podstawową płaszczyzną technologiczną, która musi być uwzględniana w pozwoleniach zintegrowanych (IPPC) jest tzw. Najlepsza Dostępna Technika (Best Available Technique-BAT). BAT została zdefiniowana w Dyrektywie 96/61/WE w sprawie zintegrowanego zapobiegania i ograniczania (kontroli) zanieczyszczeń, zwana popularnie Dyrektywą IPPC (ang. Integrated Pollution Prevention and Control). Na podstawie tej dyrektywy polskie prawo definiuje Najlepsze Dostępne Techniki (BAT)-jako najbardziej efektywny oraz zaawansowany poziom rozwoju technologii i metod prowadzenia danej działalności, wykorzystywany jako podstawa ustalania granicznych wielkości emisyjnych, mających na celu eliminowanie emisji lub, jeżeli nie jest to praktycznie możliwe, ograniczanie emisji i wpływu na środowisko jako całość
Dokumenty referencyjne Najlepszych Dostępnych Technik(BREF) dla poszczególnych branż znajdują się na stronie ministerstwa środowiska.
Stosowane rozwiązania
Wracając do zagadnienia ograniczania zapylenia na stanowisku pracy najkorzystniejszymi rozwiązaniami elementów wentylacji miejscowej wywiewnej, przeznaczonych do odsysania zanieczyszczeń są z reguły pełne obudowy. Pełne osłonięcie źródła emisji pozwala bowiem na uzyskanie wysokiej skuteczności działania urządzeń wentylacyjnych, przy odprowadzaniu najmniejszej ilości odsysanego powietrza. Gdy nie jest możliwe zastosowanie pełnych obudów, stosuje się obudowy częściowe, okapy lub ssawki są one jednak mniej skuteczne.
Konstrukcja obudów wentylacyjnych musi:
- zapewnić wygodną pracę przy obsługiwanych maszynach i urządzeniach
- uwzględniać wymagania stawiane stanowiskom pracy z punktu widzenia ergonomii
- zbudowane tak, aby nie utrudniały okresowych przeglądów oraz remontów maszyn i urządzeń technologicznych.
Niezależnie od wentylacji miejscowej wywiewnej, w pomieszczeniach gdzie wydzielane są do powietrza szkodliwe substancje musi być stosowana mechaniczna wentylacja nawiewno-wywiewna, której wydajność musi wynikać z potrzeb użytkowych i funkcji pomieszczeń, bilansu ciepła i wilgotności oraz bilansu zanieczyszczeń stałych i gazowych środowiska powietrznego. W pomieszczeniach pracy, w których wydzielają się substancje szkodliwe dla zdrowia, wentylacja powinna zapewniać stężenia tych substancji w powietrzu co najmniej poniżej wartości najwyższych dopuszczalnych stężeń tych substancji. Jeśli substancje biorące udział w procesach mogą tworzyć z powietrzem mieszaniny wybuchowe niezbędne jest aby instalacje wentylacyjne odpowiadały warunkom ustalonym ze względu na niebezpieczeństwo pożaru lub wybuchu. W takim przypadku szczególnie ważne jest prawidłowe zaprojektowanie i eksploatowanie instalacji wentylacyjnych ale także unikanie zapylenia wtórnego przez bezpylne sprzątanie osadzających się pyłów na posadzce czy konstrukcjach za pomocą centralnych instalacji odkurzania.
Przykłady stosowanych rozwiązań w najbardziej uciążliwych procesach technologicznych
Elektryczne piece łukowe
W czasie produkcji stali w elektrycznych piecach łukowych dochodzi do wydzielania znacznych ilości pyłów i szkodliwych gazów.
Zgodnie z wytycznymi dla branży odlewniczej zawartymi w PRZEWODNIKU W ZAKRESIE NAJLEPSZYCH DOSTĘPNYCH TECHNIK (NDT) z września 2005 wydanymi przez Ministerstwo Środowiska w celu ograniczenia do minimum emisji niezorganizowanej i maksymalnego wychwycenia oraz oczyszczenia gazów odlotowych z pieców łukowych zaleca się stosowanie następujących wymienionych technik:
- odciągi sklepieniowe wychwytujące gazy odlotowe emitowane z rejonu sklepienia, okna wsadowego, rynny spustowej oraz elektrod,
- boczne miejscowe odciągi gazów odlotowych emitowanych przez otwór przelotowy elektrod,
- okapy wyciągowe zlokalizowane ponad piecem łukowym i polem załadowczym kosza wsadowego,
-
bezpośredni odciąg gazów poprzez dodatkowy czwarty otwór w sklepieniu pieca,
- częściowa lub całkowita hermetyzacja pieców (systemy „dog-house”).
Stosowanie okapów wyciągowych ponad piecem i polem załadowczym nie zapewnia jednak dostatecznej hermetyzacji procesu ze względu na zbyt dużą odległość pomiędzy piecem a okapturzeniem instalacji wyciągowej. Objawia się to występowaniem niezorganizowanej emisji pyłowo-gazowej nawet w przypadku zastosowania intensywnego odciągu gazów odlotowych.
Bezpośrednie odprowadzenie gazów poprzez tzw. „czwarty otwór” wymaga z kolei zastosowania przewodów odciągowych chłodzonych wodą lub zabezpieczonych materiałami ogniotrwałymi. Dopalenie dużej ilości CO zawartego w odciąganych gazach wymaga podawania powietrza atmosferycznego do przewodu odciągowego w celu uniknięcia potencjalnej eksplozji. Wysoka temperatura odciąganych gazów stwarza konieczność zastosowania skomplikowanych systemów schładzania spalin dla ochrony filtrów tkaninowych przed uszkodzeniem. Rozwiązanie to charakteryzuje się niską wydajnością oraz przyspiesza utlenianie elektrod grafitowych.
Najbardziej efektywnym rozwiązaniem pozwalającym na wychwycenie ponad 98% emitowanych gazów odlotowych jest zastosowanie hermetyzacji jednostek piecowych poprzez wyposażenie ich w ruchome lub stałe obudowy typu ”dog-house”. Oprócz pieców łukowych zabudowa obejmuje także dół spustowy. Ruchomy strop i ściany boczne obudów umożliwiają załadunek pieca oraz odbiór ciekłej stali przy użyciu suwnicy. Emitowane gazy odlotowe są ujmowane przez główny odciąg zlokalizowany w górnej części obudowy ponad piecem, który wyposażony jest w wentylatory wyciągowe. Omawiane rozwiązanie może być udoskonalone poprzez zastosowanie dodatkowego miejscowego odciągu gazów emitowanych spod sklepienia pieca oraz wyposażenie stropu i ścian bocznych obudów „dog-house” w kurtyny powietrzne uruchamiane w trakcie załadunku i spustu metalu do kadzi. Zastosowanie pełnej hermetyzacji pracy pieców pozwala ograniczyć do minimum emisję niezorganizowaną oraz natężenie hałasu na stanowiskach zlokalizowanych w obrębie oddziałów topienia do poziomu około 85 dB(A). Zużycie energii przez instalację typu „dog-house” jest około 30-50% niższe od energii wykorzystywanej przez systemy odciągowe wyposażone w okapy wyciągowe.
Obudowy typu dog hause były zainstalowane w ABB Zamech w Elblągu oraz w Hucie Mała Panew w Ozimku.
Przykładem nowatorskiego podejścia do ograniczenia emisji pyłów jest rozwiązanie według wynalazku inżyniera Jana Lenartowicza „Odciąg gazów i pyłów z elektrycznych pieców łukowych” (Sposób i kształtka do uszczelnienia otworu elektrodowego łukowego pieca elektrycznego) Zastosowanie nowoczesnego sposobu uszczelnienia obszarów wokół elektrod na sklepieniu pieca z równoczesnym obniżeniem temperatury spalin, opracowano na podstawie wiedzy, doświadczeń i rozwiązań chronionych prawem wynalazczym. Wynalazek zabezpiecza przed nadmiernymi wyrzutami pyłów w trakcie najintensywniejszej pracy pieca, jak też wpływa na częściowe obniżenie temp. spalin, wydłużając czas pracy elementów znajdujących się w obszarze elektrod, uchwytów prądowych, instalacji chłodzenia wodnego elektrod czy konstrukcji sklepienia.
Elektryczne piece indukcyjne
Podobnie jak w przypadku pieców łukowych, w trakcie wytapiania stali w piecach indukcyjnych zgodnie z BAT należy zapewnić warunki do maksymalnego odciągu gazów odlotowych i ich oczyszczenia. Zaleca się zastosowanie jednej z następujących technik:
- wykorzystanie systemu ogólnej wentylacji oddziału wytapiania,
- użycie okapów wyciągowych ponad piecem,
- zastosowanie stałych i ruchomych odciągów bocznych,
- wykorzystanie odciągów pierścieniowych zabudowanych bezpośrednio przy pokrywie pieca.
Odpylanie pieców indukcyjnych odbywało się przez wiele lat za pomocą górnych stałych lub obrotowych okapów odciągowych. Skuteczność ujmowania zanieczyszczeń przez stałe górne okapy zależała od ich lokalizacji (wysokości nad piecem) i ilości odciąganego powietrza. Najczęściej okapy były zawieszane wysoko i nie ujmowały całości emitowanych zanieczyszczeń (im wyżej tym okap a tym samym ilość odciąganego powietrza musiały być większe) co wymagało dużych nakładów inwestycyjnych i eksploatacyjnych. Często stosowanym rozwiązaniem były okapy obrotowe, gdzie wyeliminowano problem wysokości okapu nad piecem ale niestety skuteczne były tylko w trakcie topienia. Przy załadunku wsadu i spuście metalu okapy okazały się mało skuteczne – nie było możliwości ustawienia okapu (ze względu na zawiesie suwnicy) bezpośrednio nad źródłem pylenia. Najbardziej skuteczne okazały się okapy, które były integralną częścią pokrywy pieca. Króciec podłączeniowy do instalacji odpylającej zlokalizowany był w osi obrotu pieca. Kolejnym rozwiązaniem zmniejszającym emisję pyłów do otoczenia była zmiana załadunku wsadu : z załadunku suwnicą na załadunek specjalnie skonstruowanym wozem załadowczym, gdzie załadunek wsadu był całkowicie zhermetyzowany a odciąg odbywał się tym samym okapem, ale znajdującym się w innym położeniu.
Kraty wstrząsowe
Przy usuwaniu (wybijaniu) masy formierskiej i rdzeniowej z odlewu ma miejsce intensywne wydzielanie się pyłu, jako że formy, przynajmniej częściowo, muszą być kruszone (rozbijane).
Techniki stosowane do wychwytywania emisji z procesu wybijania zależy od stopnia mechanizacji, wielkości i rodzaju emisji oraz wielkości odlewów, szczególnie w przypadku gdy na tym samym urządzeniu (Kraty wstrząsowe) wybijane są najmniejsze i największe odlewy. Najczęściej stosuje się system ograniczania emisji obejmujący zespół wentylatorów po stronie kraty wstrząsowej. Zwykle zestawy wentylatorów są instalowane po obu stronach wstrząsarki niezależnie od wielkości kraty. Jeżeli jest to możliwe, od tyłu krata jest zamknięta w ten sam sposób. Najczęściej punkt odbioru emitowanych gazów jest umieszczony nad kratą, a gazy są odprowadzane przez przewód. Może występować zagrożenie porywania wraz z gazami masy jeżeli przewód ssący umieszczony będzie zbyt blisko odlewu. Najlepszym sposobem uzyskania odpowiednio niskiej emisji przy stosunkowo małej wydajności wentylatorów jest prowadzenie operacji wybijania w zamkniętej obudowie. Otwierany dach, drzwi oraz rynny zsypowe umożliwiają stosowanie suwnic lub innych urządzeń transportujących odlewy. Ponadto prowadzenie wybijania w zamkniętej kabinie zmniejsza poziom hałasu.
Najlepsza dostępna technika mówi o zapewnieniu poziomu emisji pyłów rzędu 10 mg/Nm3 jako średnia godzinowa.
Jeśli chodzi o wychwytywanie pyłów i gazów odlotowych z procesów wykańczania odlewów to przy stosowaniu do wykańczania technik termicznych (cięcie palnikiem acetylenowo -tlenowym, elektrożłobienia, spawalni, itp.) mogą być wychwycone i usunięte znaczne ilości pyłów i dymów. Stanowisko pracy może być tak obudowane, aby zapewnić pracownikowi swobodę ruchu i dopływ świeżego powietrza (np. kabiny).
Techniki wychwytywania pyłów w czasie cięcia ściernicą i szlifowania zależne są od używanego oprzyrządowania. W przypadku urządzeń stacjonarnych zazwyczaj stosuje się okapy częściowo obudowane pozwalające odciągać zanieczyszczenia do komina odciągowego.
W przypadku użycia narzędzi ręcznych (np. przy obróbce odlewów wielkogabarytowych) usuwanie pyłów jest utrudnione. Wówczas sporadycznie stosuje się odciągi przyłączone do osłony tarczy (metoda mało popularna ze względu na rosnący ciężar narzędzia i utrudnione możliwości manewrowania nim).
- oczyszczanie odlewów (oczyszczarki pneumatyczne, wirnikowe, inne): proces prowadzony w zamkniętych kabinach, gdzie generowana jest duża ilość pyłów.
- przecinanie,cięcie: powstająca w procesach cieplnych emisja (pyły, dymy) jest wychwytywana najczęściej z obudowanych stanowisk (kabin). Ważne jest aby instalacje wychwytujące umieścić możliwie blisko źródła emisji. Przy prawidłowym rozmieszczeniu wyciągów powietrze zawierające pyły jest usuwane bezpośrednio z przestrzeni, którą oddycha pracownik.
- szlifowania odlewów: w przypadku stosowania urządzeń stacjonarnych wykorzystuje się odciągi; przy ręcznym szlifowaniu stosuje się zazwyczaj obudowane stanowiska pracy z zastosowaniem ścian odciągowych.
- spawanie: w zależności od rodzaju produkowanych odlewów i stosowanych technik spawalniczych może zachodzić większa lub mniejsza emisja, która najlepiej wychwytywana jest przez ruchome ramiona odciągowe.
Podsumowanie
W związku z przyjmowaniem przez Polskę obowiązujących w krajach Unii Europejskiej aktów prawnych i normatywów dotyczących ochrony środowiska, musi następować dalsza zmiana warunków, w których przyjdzie funkcjonować zakładom przemysłowym. Coraz większą uwagę trzeba będzie zwracać na zminimalizowanie negatywnego oddziaływania przedsiębiorstwa na środowisko naturalne oraz na zapewnienie pracownikom jak najlepszych warunków pracy. Działania w tym kierunku,jak wskazują doświadczenia innych krajów UE, przynoszą wymierne korzyści ekonomiczne, wynikające z ograniczenia zachorowalności osób zatrudnionych przy produkcji, a także zmniejszenia opłat naliczanych z tytułu zanieczyszczania środowiska. W działaniach tych olbrzymią rolę odgrywać będzie stosowanie coraz doskonalszych technik odpylania bez których niemożliwa jest jakakolwiek produkcja związana z zapyleniem.
Obowiązujące w Polsce normy w zakresie najwyższych dopuszczalnych stężeń czynników szkodliwych dla zdrowia w środowisku pracy są w przeważającym stopniu zgodne z normami jakie zostały ustalone w krajach Unii Europejskiej i USA, w niektórych przypadkach są nawet ostrzejsze. Zatem zdrowie i życie pracowników krajowych zakładów przemysłowych nie będzie zagrożone, pod warunkiem ścisłego przestrzegania tych norm.
Literatura
- Marzena Smolarek – Ograniczenie zapylenia na stanowiskach pracy-Bezpieczeństwo Pracy 12/2006
- Maciej Gliński –Zapobieganie niewłaściwym parametrom mikroklimatu- rozwiązania techniczne i organizacyjne – Bezpieczeństwo Pracy 12/2002
- Krzykowski R. K. Trenczek S. – Przeciwdziałanie skutkom zapylenia obiektów przemysłowych w sektorze energetycznym – Zeszyt Naukowy IGSMiE PAN –zeszyt 78/2010
- Janusz Zajączkowski – Odpylanie w przemyśle
- Maciej Gliński-Optymalizacja parametrów powietrza w pomieszczeniach pracy miejscowa wentylacja wywiewna- PORADNIK
Autor artykułu: Regina Kowalczyk, GRUPA WOLFF